Three big data lessons we can learn from manufacturing
Smart Factories are using big data analytics to become more productive and sustainable. Agriculture can do this too.
Manufacturers are leveraging big data analytics to improve their bottom lines. At times, the results have been spectacular. Maintenance costs reduced by 40%, capacity increased by 10%, yields up 50%. Here, we discuss three lessons which our sector could learn from theirs.
Manufacturing and agri-food share a number of similarities. They are both based around the production of goods or produce; both must negotiate a complex, multi-faceted supply chain; both have become increasingly reliant on technology. The Internet of Things (IOT) and Big Data Analytics have become familiar terms in both sectors, if not always fully understood.
They also face similar challenges. In order to compete with emerging economies, they are being forced to produce better-quality goods in larger volumes for a lower cost. At the same time, they are being asked to be more sustainable, which has meant phasing out some tools and practices known to increase productivity. Radical solutions are needed.
Agri-food can learn a lot from studying the practices of leading manufacturers, this article lays out 3 of them.
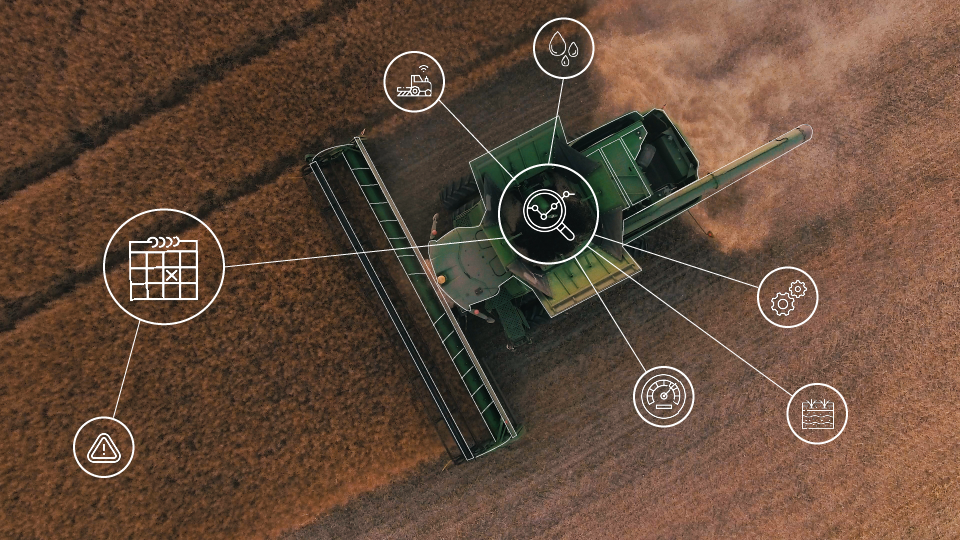
1. Predictive maintenance
A haphazard approach to machinery maintenance and a ‘run to failure’ mentality permeates in parts of both industries. In some instances (where machinery is low cost and replacements or spares available) this strategy may be appropriate, but for high-value or business critical machinery, breakdowns are costly.
Unplanned downtime and poor maintenance strategies can reduce a manufacturers productive capacity by 5 – 20%*. Necessarily, this has drawn the attention of those seeking to improve performance. That attention has resulted in the rise of predictive maintenance.
Modern ‘Smart factories’ contain thousands of sensors positioned throughout the manufacturing process, these sensors send a constant stream of information back to the cloud. This operational data can be analysed, and patterns identified. Predictive algorithms monitoring real-time sensor data can flag upcoming breakdowns well in advance.
Preventative maintenance can then be scheduled into planned-downtime. At worst, repair bills can be minimised by shutting off machinery before further damage is caused. At best, factories run on maximum capacity 24/7.
Digital Twins
Predictive Maintenance has been successfully deployed beyond the shop floors of major factories. Manufacturers of consumer electronics have benefited too, with the help of Digital Twins.
Digital Twins are digital replicas of physical assets (the physical twin). Data is transmitted seamlessly between the two, creating an accurate digital representation of how the device is operating, the user’s behaviour, and the device’s performance.
By analysing vast amounts of data, patterns leading up to breakdowns can be identified. Once these patterns are understood, predictive algorithms can notify product users of potential problems, before their device breaks down.
Takeaway
Many modern farms are as reliant on technology as manufacturing plants – breakdowns can be just at catastrophic. Techniques which have enabled some manufacturing plants to reduce maintenance costs by 40%* can be applied to agriculture too.
For Farmers
Farmers should have a preventative maintenance plan in place, which includes regular servicing, cleaning, and checks. Many farms will already be doing this, these farms will still be experiencing breakdowns.
This is because they are operating on imperfect information. Without analytics, preventative maintenance is little more than educated guess work. For agriculture to realise the same benefits being enjoyed by manufacturing, insights from big data analytics are required.
In order for this to happen, farms must be willing to share real-time data regarding on-farm operations and machinery performance with relevant organisations; something many farms have been historically unwilling to do.
Farmers are right to be protective of their data. Organisations they share it with should be vetted, but for agriculture to enjoy the same benefits as manufacturing, attitudinal change around data sharing is required
For suppliers
Platforms like MyJohnDeere and AGCO Fuse are already collecting real-time data from on-farm operations. Sensor technology is already being deployed on combine harvesters to monitor yield, grain loss, load, and blockages. Yet these are not the only factors influencing the likelihood of machinery breakdown: crop, weather, soil type, elevation, and cultivation methods all play a part.
For predictive maintenance to become a reality, all of the relevant variables must be brought together in one place, held in the correct formats, and subjected to rigorous analysis. Much of this data is already available, but accessing it is resource intensive.
Agrimetrics is working to make this information more easily available. Innovative agri-tech organisations should take advantage. In terms of identifying pain-points, combine breakdowns during harvest are up there with the most excruciating; the afflicted will pay to be cured – and everyone will benefit.
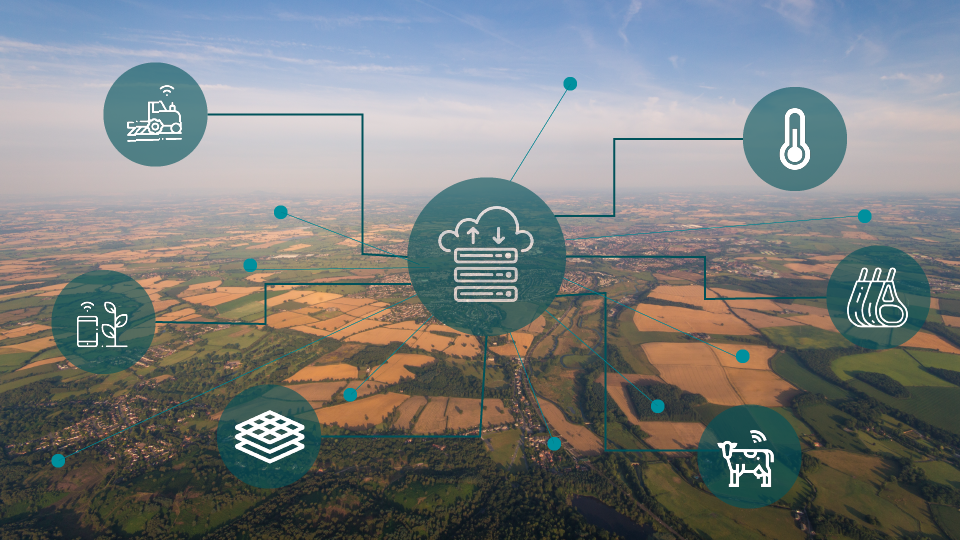
2. Interoperability and the Internet of Things
The Internet of Things (IOT) and manufacturing have converged. New machinery, robotics and automation have driven huge gains in manufacturing productivity. General Motors alone operates more than 13,000 connected robots operating across 54 plants.*
That connection – not robotics – is key. The impact of new machinery, however advanced, is limited when operated in silos. Value comes from connecting and analysing huge volumes of data originating from data points spread across the whole production process.* For example, a packaging robot may pack more items per minute than a human operator, but a fully connected ecosystem enables the creation of fully automated production lines; the benefits of the latter being exponentially greater than the former.
The ability for internal production systems to communicate with customer ordering systems, suppliers, and inventories has been foundational to the make-to-order and just-in-time manufacturing models which are now best practice in the sector; models which have allowed the automotive industry to save $1,200 per vehicle.*
Even without significant upfront investment in robotics and advanced technology, merely collecting and analysing data can deliver important insights. In turn, these insights can be used to make better management decisions, improving productivity.* Strategically, connecting existing devices and making effective use of their outputs may yield a higher ROI than purchasing new, siloed machinary.
Takeaway
Agriculture has already adopted the IOT; unfortunately, its component siblings are estranged. In a recent whitepaper produced by Agrimetrics for the Food & Drink Sector Council’s Agricultural Productivity Working Group, lack of interoperability was cited as a key challenge preventing the sharing and use of data.
The lack of common standards for interoperability creates significant overhead for farmers. Data-entry is often manual; double-entry is common. Data is held in multiple systems and in different formats. The greatest benefits come when insights are derived from large volumes of connected data, drawn from multiple sources; but the cost of combining this data is significant – few see it as a valuable investment.
For Farmers
Interoperability should be a key factor influencing new purchase decisions. Farmers should recognise that the value of a piece of kit extends beyond its operational utility – the ability of that kit to link with other devices is key to unlocking the greatest overall benefits for the farm.
Rather than an unnecessary evil, farm management software should be considered an essential piece of kit too, as it is vital for collecting and presenting data. In turn, this can improve on-farm decision making.
Unfortunately, even with all the will (and budget) in the world, creating a fully-connected Smart Farm is virtually impossible – devices, software and machinery available on today’s market simply aren’t interoperable.
However, manufacturers will respond to market pressures. If farmers demand a connected internet of things, suppliers will deliver.
For suppliers
Interoperability benefits industry too. So long as data is locked away in standalone tools, it remains out-of-bounds to organisations who would otherwise convert that data into value.
Industry has as much to gain as farmers from higher levels of connectivity in the IOT. It would enable retailers to promote traceability, app-developers to monitor product usage, wholesalers to improve supply chains. Yet there is little movement towards common standards.
Lessons can be learned from New Zealand, where data standards have been co-developed between dairy farmers, industry and government. Until that happens, improved interoperability can at least be achieved on a project-by-project basis, by working with specialists such as Agrimetrics, who are developing a platform which will link data-sets from across the agri-food industry.
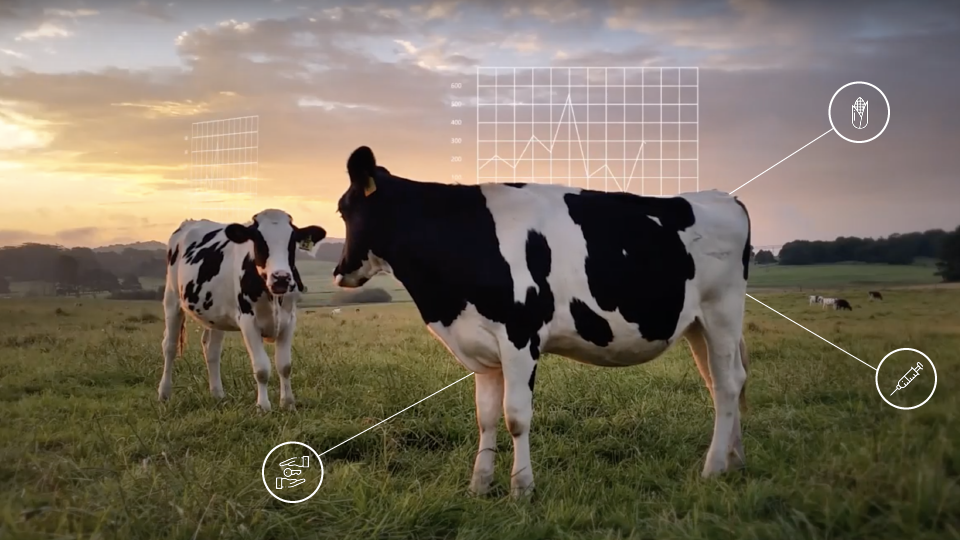
3. Next level overhead tracking
Profit margins are hard fought in the manufacturing sector. In 2017, Forbes ranked elements of the sector as some of the worst performing in terms of net profit, alongside publishing and farm product wholesalers.* The drive to improve profitability has long motivated the industry to look hard at their costs of production; reducing these costs directly impacts the bottom line.
Cost tracking is fundamental to any business’s success. It is used to inform pricing strategies and ensures liquidity. This information is essential for managers wishing to cut costs. Yet many organisations have only a basic understanding of their overheads, built around a descriptive view of their numbers. Labour costs, for example, may be understood in terms of a wage bill. Production costs are a cumulation of the most visible metrics, such as raw materials, rents, wages, etc. In both cases, there is little understanding of the full suite of factors influencing these costs.
Focus on the minutia
With labour costs accounting for such a large proportion of overheads (c.40% for the average manufacturer) even small improvements can improve profitability. This has driven manufacturing organisations to explore new ways of using big data analytics to identify improvements.
One area is in recruiting. Cornerstone, a talent management platform, analyses multiple data points – including personality type and commuting times – to make predictions on employee performance. This method enabled Xerox to reduce the number of employees leaving within 6 months (the timeframe required to recoup recruitment costs) by 20%.*
More controversially, “smart badges” have been utilised by some organisations to monitor employee movements and actions. One company found that employees who took breaks together performed better than those who did not; by instituting a group break policy, performance improved by 23%.*
Some smart badges can be GPS enabled. Combined with sensors fitted throughout the factory, some manufacturing plants have built a picture of the cost associated with each task. Efficiency savings can be found simply by relocating machinery to decrease the amount of time operators and engineers spend travelling.
Takeaway
Smart badges may not be appropriate (or desirable) for many agri-food organisations; however, the commitment of some manufacturers to fully understanding their costs – and the factors impacting these costs – is something all businesses could take on board.
For Farmers
For many businesses, tracking even relatively basic costs would yield benefits. A 2018 survey by DEFRA found that 60% of 2,700 surveyed farm holdings did not use any financial management software. At best, the results from this survey indicate farms are tracking costs in an inefficient way (e.g. spreadsheets or paper journals); more likely, it suggests that farms are hardly tracking costs at all.
If costs are not well understood, then initiatives to cut costs and improve profitability are less likely to succeed. A range of software options now exist which enable farms to monitor their costs more closely. Fuel, depreciation, machinery maintenance, and operator costs can be collected and broken down by task. The performance of individual cattle can be monitored too. Farm businesses who are collecting data and using insights from that data in their decision-making process, are more profitable.
For suppliers
The process of tracking costs is laborious for farm businesses. Suppliers can do more to streamline processes. The bulk of data collection and analysis can and should be automated. Ordering systems should integrate with accounts packages, which in turn could incorporate data from machine controllers, which often collect valuable information such as running costs and application data.
Rather than lamenting farm businesses for not monitoring their costs more effectively, organisations should see this as an opportunity to solve an industry pain point through innovation and product development.
Time to learn quickly
The full implications of ELMS are still unclear, so too are the ramifications of Brexit. What we do know, however, is that the UK agricultural sector needs to improve productivity. Just like in manufacturing, farms are being asked to sustainably produce better-quality goods in larger volumes for a lower cost; just like in manufacturing, big data analytics holds the key.
Other articles that might interest you
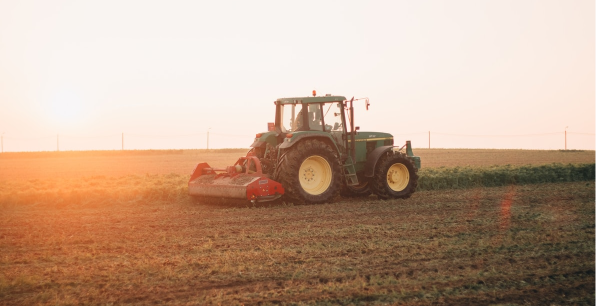
AI identifies crops from space with 90% accuracy
Agrimetrics launches CropLens AI, a proprietary algorithm that identifies crop types from space.
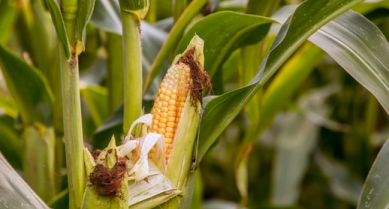
ClearSky: Cloud free satellite data for agriculture
ClearSky's artificial intelligence removes a major barrier to the efficacy of satellite
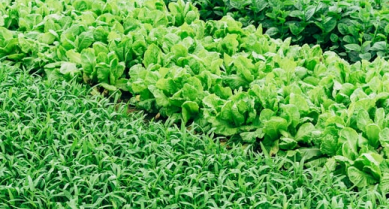
ClearSky: Cloud free satellite data for agriculture
ClearSky's artificial intelligence removes a major barrier to the efficacy of satellite
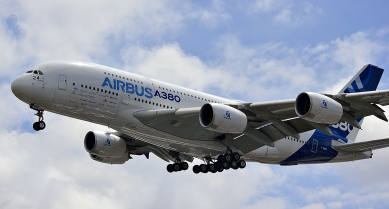
Agrimetrics partners with Airbus to reduce cost
Crop Analytics, a crop and field analytics package from Airbus, is now available at a new, lower price.